But we all have to start somewhere and so I asked a young blacksmith, who had just started his career in armormaking, to build me a helmet after my (vague) specifications.
And only a few days before Christmas I received word that the deed was done:
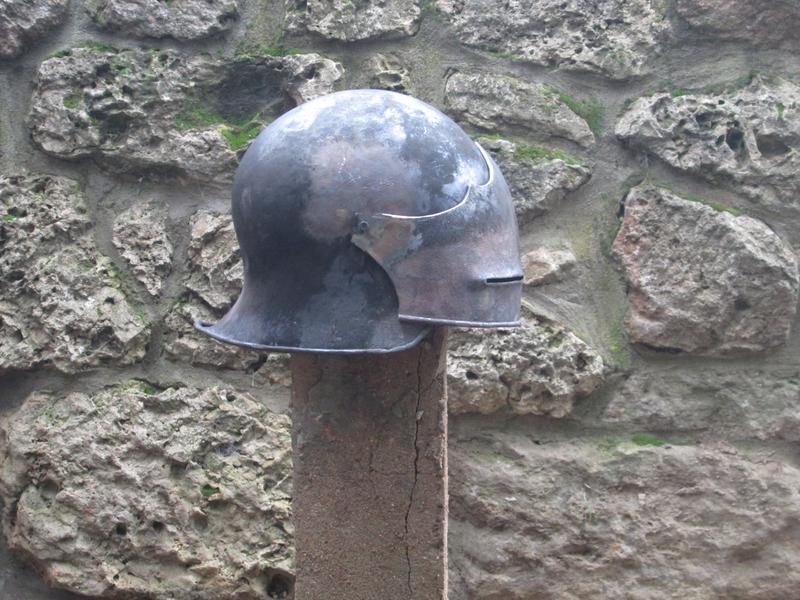
The helmet is of course not finished - I want to polish it myself, based on historical armor polishing methods, so the smith only planished it and on the photos it still lacks a few finishing touches from him.
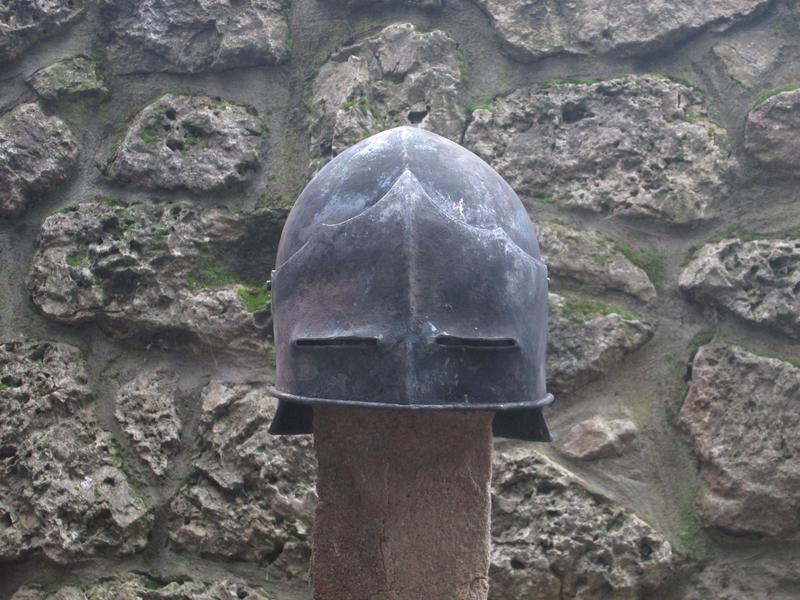
It is based on several examples from various artistic sources of the 1440-1460.
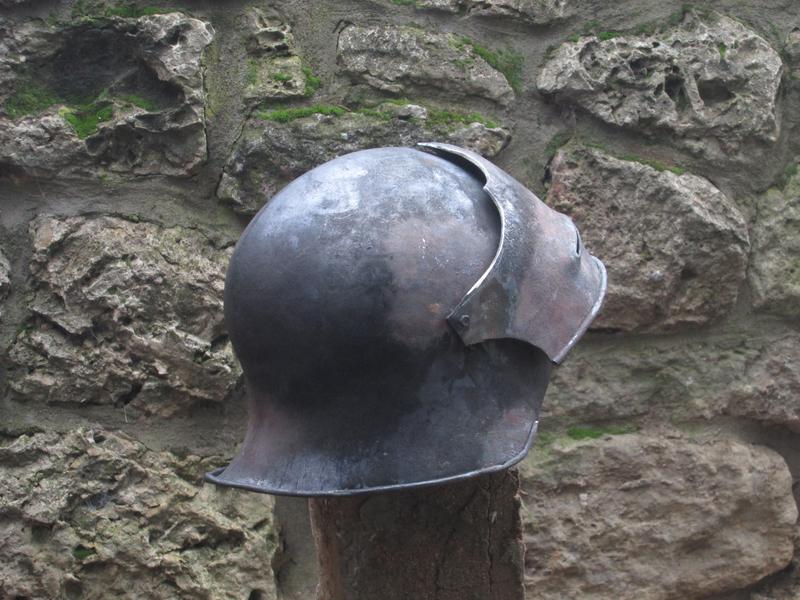
Polishing, drilling the holes for the lining rivets and permanently attaching the visor will be done by me.
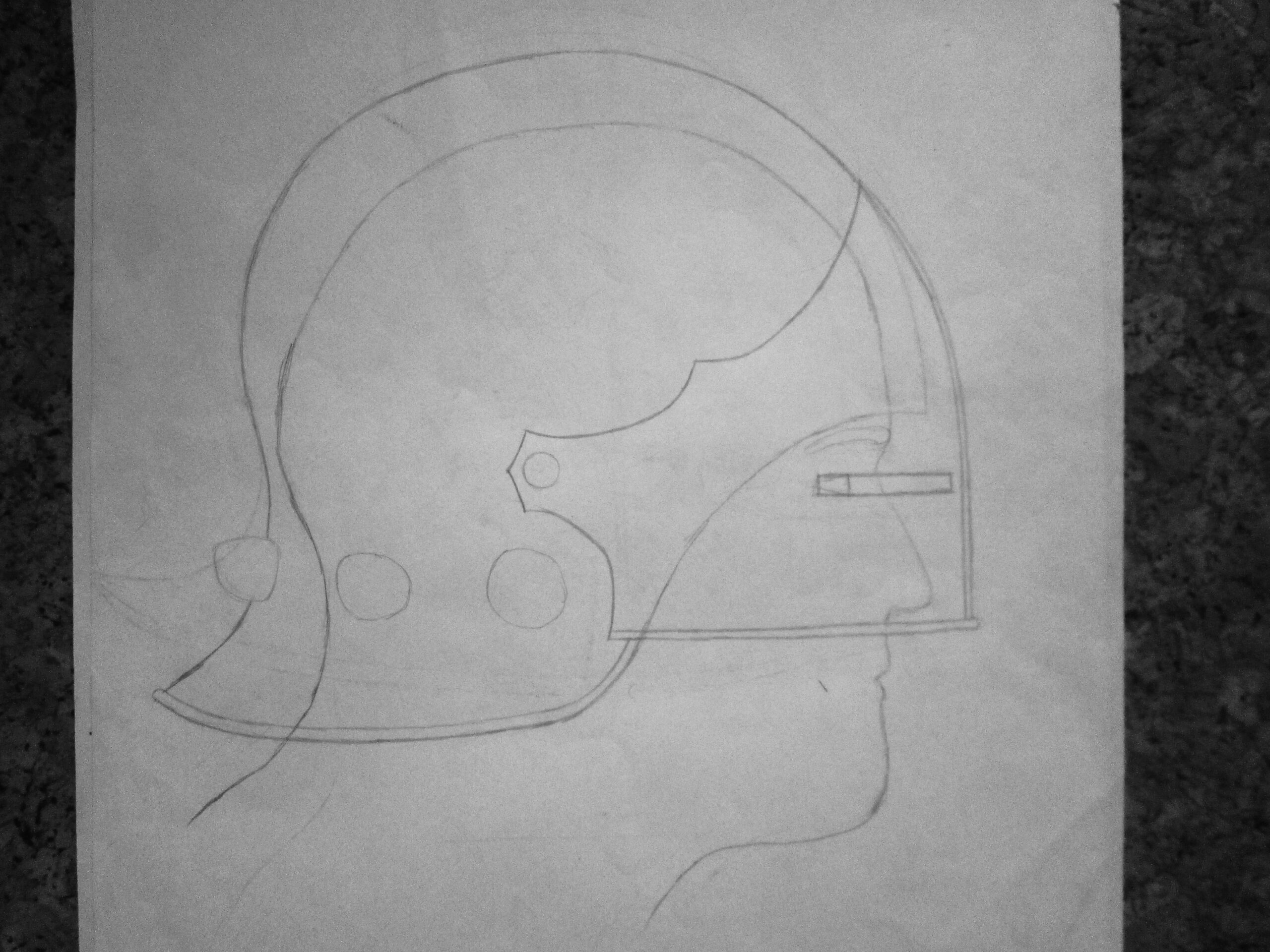
As the sketch shows it just covers the nose.
So of course the next step, after fitting a liner, will be a mail bevor that goes over the mouth - a solution that one sees a lot in artwork of this period.
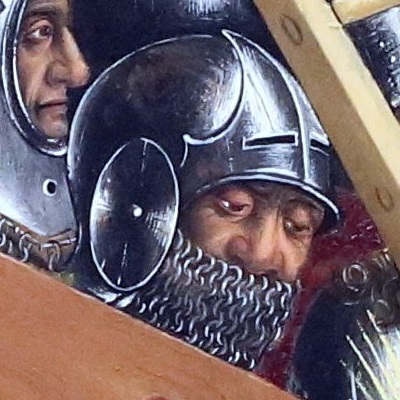
(Karlsruhe Passion, 1450-55)
That's the first problem - how do these things hold up? One solution could be that they are fastened to the lining leather of the helmet or that they are attached to a "cap" worn under the helmet. For practical reasons I think I go with the latter.
To achieve the shown fit it would be possible that they were open in the back and fastened.
For torso protection I want to make a padded jack of the, as I call it, Zebra style - it's basically the reason why I want to build this kit.
(I started a thread about these garments nearly 4 years ago: http://forums.armourarchive.org/phpBB2/ ... ?p=2811385 )
It's a sleeveless padded garment, with vertical quilting that is painted with black stripes parallel to the quilt lines.
Because of the mail bevor it will remain without a collar. The red woolen fringes at the armholes are a must.
It is worn over either a shirt of mail or mail sleeves and either a skirt or brayette. I already have the basis for sleeves and a skirt.
Above it goes a breastplate with a fauld and maybe tassets. The breastplate should either be an "older" model or a simple infantry variant.
That is problem number two - I'm not sure yet how the breastplate should look.
The shoulders, arms and gauntlets should be based on this roman soldier dressed in a fancy Zebra-jack who guides Longinus' spear:
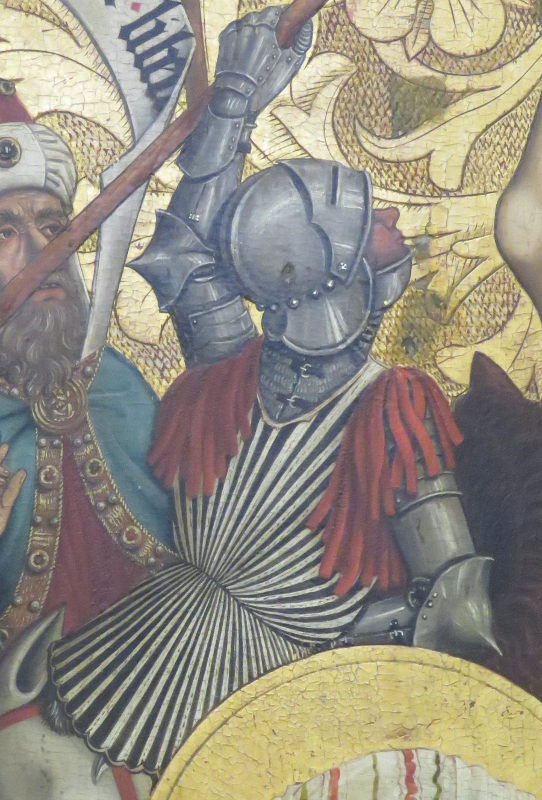
(A crowd at calvary, 1460)
They are simple designs, well suited for the intended project.
The legs are the last of my worries.
I will commission all, or most, plate armor parts (as I did with the helmet) because I am many things - but armorer is not among them

But as with the helmet I want to apply the finishing touches - polishing, mounting fabric and leather, maybe surface treatment.
Everything made of fabric I do myself.
Everything made of mail I will try to build myself. And if I fail heroically I guess I will also commission these parts.
But first: Finishing the helmet as sonn as I can pick it up.
Any questions or tips?
Anyone has an idea how the breastplate could look like or something to add about the mail bevor?
I will give further details about the construction of the helmet, but I have to ask the smith first how he did it - but if he wants, he could say a few words himself.